
FUEL SYSTEM TROUBLESHOOTING
As more and more setups include aftermarket fuel systems, there is an increasing need for troubleshooting these fuel systems. The following is a simple procedure I have used for decades, and I have added to it over the years as I run into bizarre new problems. I will attempt to explain what each step is trying to accomplish, but knowing how these fuel systems work is really the best bet in effective troubleshooting. In many cases, that knowledge is expanded for people after they run through this procedure a few times and see how things work. This is taken from something I've written with ECMlink DSMs in mind as part of a pre-tune checklist, but it does transfer well to any setup. I will add more info to this to help explain things further.
Base Fuel Pressure:
​
This is something that is still often misunderstood. Simply put, it is Fuel Pressure minus Manifold Pressure, or the actual differential pressure across the fuel injector. It should be the same value at all times, regardless of running conditions, with the exception of the expected brief delays in response during transient conditions. Logging a fuel pressure sensor in ECMlink makes this a no brainer, because the software will do this math for you and provide a Base Fuel Pressure loggable parameter. It should be a flat line, from idle, through cruise, and all the way through WOT! Rather than using a haphazard looking fuel pressure trace and trying to compare it to boost, just look at this Base Fuel Pressure parameter. Anywhere it's not a flat line quickly highlights an issue. A drop at WOT of a few psi is typical however and not cause for alarm.
​
Base fuel pressure needs to be set correctly, and FPR/pump/return line functionality verified before tuning any car. Most people will simply start at 42-43 psi and be good to go. Others will run more or less base pressure, but you have to be sure you understand the implications of doing this. Always run it by your tuner.
​
​
The following is the procedure I use to verify operation of the fuel system:
​
-
Kick the fuel pump on in ECMlink, Misc tab. Turn the FPR set screw in all the way, or until you achieve ~80 psi (different FPRs have different maximums, consult the documentation for your particular regulator. You should be able to achieve a pressure very near the top end of the base fuel pressure range given by the manufacturer for the spring installed.). This verifies FPR spring pressure, and that the pump assembly has no leaks. Blown out pump hat o-rings or split supply hoses inside the tank often won't let you get over ~50 psi. These are leaks that you'll never see otherwise, and they do happen. It is also possible to have a weak pump, or weak pump wiring show up as a problem here.
-
Back the FPR screw all the way out. This verifies return line functionality and orifice size. Ideally you will be able to get down to 20-25 psi. This doesn't guarantee you aren't over running the return line, but it's a start. More on this below.
-
Set base pressure back to 42-43 psi.
-
Apply 40 psi shop air to the FPR reference port. You should see 82 psi. If not, check for boost leaks in the FPR. A simple jig can be assembled with a good mini-regulator with a 0-60 psi gauge for good resolution, hooked up to shop air (see picture below). In the absence of this, the gauge on your compressor will probably get you close, but don't expect it to be more accurate than about 5 psi.
-
If possible, apply 20”hg vacuum to the reference port with a mightyvac. You should see pressure drop 10 psi, to 32. If not, check for leaks, or for over running the return line (a larger line or regulator orifice may be required, more on this below).
-
Reattach the reference line and start the car. Note idle vacuum and subtract it from your set base pressure (2”hg = 1 psi). This should be the pressure you see at idle. If not, check for leaks or return line over run as in step 5. Example: 43 psi base, and 20" hg idle vacuum. 20" is -10psi, so you should see 33 psi fuel pressure in this case.
-
If fuel flow from the pump, or through the filter/lines, etc, is a concern, you can also flow test the pump. The easiest way is to run the return line into a 5 gallon fuel jug, kick the pump on in ECMlink, and time how long it takes to move the fuel. You can time it in one gallon increments and do it a few times to be sure you're getting repeatable results, or time it over a larger volume like 3-4 gallons which also increases the accuracy of the test. It's not perfect, but it will highlight a shit pump pretty handily. Note that most plastic fuel jugs will expand with time, making 1 gallon on the markings actually more than one gallon. Also make a note of the battery voltage during the test. If your gobshyte small battery or other POS you have in there isn't a solid 12v+ it will affect the results. It doesn't hurt to put a battery charger on it for the test (5-8 amps at least, trickle chargers will not help). In my experience, I always get VERY close to the advertised flow ratings of the pumps I test, when they are working. By taking the measurement at the return line, you're including the filters and lines and fittings in the test! You can also test at various pressure by adjusting the screw manually to what you want for the test. Some pumps may pass at 43 psi, but shit the bed at higher pressures.
-
If all of this passes, you can be reasonably sure that the fuel pressure control system will function as expected. There are a small percentage of potential issues that can still sneak by this test of course. It's still always a good idea to log fuel pressure, since it will show any of a large number of possible problems easily, with no guessing. It will also make step 6 much easier, just stream data and look at the Base Fuel Pressure parameter.
Test rig, with a 0-60 psi mini-regulator, quick connect for shop air, and a few options for connecting to the FPR, wastegates, pressure sensors, etc.
​
​
​
​
​
​
​
​
​
​
​
​
A note on return line capacity and regulator orifice size.
​
Normally, over running the fuel return line or regulator orifice results in too much base pressure. Either your desired base pressure can't be achieved, or your base pressure minus manifold vacuum does not go low enough. This is obvious of course. However, it is possible in rare instances to achieve a proper base pressure, and idle fuel pressure, yet still be outflowing the return line or orifice. This can cause a lean condition at WOT that can be difficult to troubleshoot. With a fuel pressure sensor, it will show up as a drop in base pressure at WOT. The usual suspected cause for dropping base pressure at WOT is a fuel supply deficiency, but in this case, it's caused by return line or FPR orifice over-run requiring you to back the set screw on the regulator out further than it really should be to achieve your base/idle fuel pressure. Once flow increases at WOT, return fuel flow drops, and you get "on the spring" in the regulator, your base pressure is now too low. Upgrading the return line or orifice size (usually requires changing regulators, though some newer regulators offer interchangeable orifices) will clear this up. It's rare, but it happens. 2G AWD cars are more often affected by this thanks to the fuel siphon valve in the pump hanger.
​
This is an example of base fuel pressure drop under load as a result of too small a return line or FPR orifice.
​
​
​
​
​
This is an example of good base fuel pressure. Nice and flat under load, just a slight blip up at throttle lift while the FPR reacts to changing fuel consumption and manifold pressure.
​
​
​
​
​
​
​
This is an example of a more typical fuel pressure shortage, to compare with the FPR example above. This was the result of having to little fuel in the tank on a pull. There is a clear and sharp drop in pressure with a corresponding lean spike in AFR. If the cause is too little fuel pump capacity, the pressure will fall off shaprly at higher airflow and not recover until airflow drops.
​
​
​
​
​
​
​
The typical small regulators used (Aeromotive A1000 and clones, small Fuel Lab, etc) have an orifice just over an 8th inch. These often do not flow enough for 450/525 pumps, particularly on 2g AWD tanks with the siphon drilled to 1/8th or 9/64th. The Aermotive X1 13303 with .188" orifice is close on a 450, too small on a 525 on some cars. The 13305 with .313 orifice is a better choice. This seems to be the go to choice right now for a 2g with a 450/525 pump. Weldon also has an FPR in .250" size that is likely a good fit.
​
Logging fuel pressure sensors in ECMlink:
​
There is no arguing that logging a fuel pressure sensor, and using the Base Fuel Pressure parameter in ECMlink, is a huge advantage to anyone willing to make the effort to install one. It will easily point out issues at a glance, eliminating hours of troubleshooting, which usually means throwing parts at the car, often costing more than the pressure sensor would have cost in the first place. And, once installed, you'll always have it. You can also move that sensor around if you're creative and log oil pressure, IC pressure drop, any number of things, very easily.
​
In general, a 0-100psig sensor is best for most people. In my case, I run a 150 psig sensor, which covers me to 60 psi boost and 90 psi base pressure. Consider your likely base pressure and boost pressure ranges and choose accordingly. One advtantage to a 0-100 psig sensor is that if it uses a 0.5-4.5v output range, you can simply select the Autometer 2246 sensor in the drop down.
​
The Autometer 2246 stainless 0-100psig sensor is a popular choice. It uses the typical 3 pin round metripack connector, but does not come with one, so you'll need to source one. It's about 100 dollars. It's a high quality sensor, from Klavico if I recall correctly.
​
AEM's 0-100psig stainless sensor, part number 30-2130-100, is about 150 dollars. It's a high quality SSI sensor and will, in my experience, last pretty much forever. I have these sensors still running at 15 years old. It does come with the connector, and you can use the same ECMlink drop down option for the 2246 sensor since they share the same scaling.
​
AEM's 0-100 psig brass sensor, part number 30-2131-100, is similar to the stainless version, but brass, and much cheaper at ~65 bucks. But, it will not last as a fuel pressure sensor. It comes with the connector and uses the same scalings as above, but is not recommended at all.
​
There are a number of cheap sensors now available as well. They can be made to work, with vary levels of success. The risk is yours to take. I would aim for something stainless, and be sure it comes with scaling information.
Once you have the sensor, you'll need to wire it to a spare input (there are plenty of write ups online showing how to do this, I won't duplicate them here), and set it up in ECMlink as a fuel pressure sensor (linear fuel pressure sensor for custom ranges) on the inputs tab, which makes it loggable and will automatically make it work with the Base Fuel Pressure display item. It will also need to be setup in the logger display if it's a custom linear fuel pressure sensor to show the correct pressure. In all case, using the above mentioned shop air jig will allow you to verify the readings up and down the sensor's range, if you want further peace of mind. This little bit of work will pay off in the long run. It'll change your life, just do it.
Other unusual issues and thoughts:
​
-
It's entirely possible to have weak connections at the pump causing issues that are difficult to diagnose. Poor contacts, bad or missing grounds, wires with all but one strand broken, things of this nature. Often they will pass continuity and voltage tests! It pays to have a good handle on electrical theory here, it's beyond the scope of this article unfortunately. But, just being aware of this possibility can help a number of people out. Good luck!
-
Dual/staged pumps can require the use of check valves on at least the secondary pump's output, if the pumps don't have them built in. There are a number of ways for this to go wrong. I may expand on this later.
-
ECMlink nitrous outputs can be used to activate staged secondary fuel pumps, or dual speed pumps (like fuel lab), I've done both and it works well when done right. Also lots of ways to go wrong here though, I may expand on this later.
​
​
Line sizing:
​
For ~10 years now I've been dealing with this unusual wave in AFR that doesn't make sense to tune out (if you do you end up with a bizarre wave in VE or MAFcomp). I'll give an example of these situations below. It used to be very rare, but has become an epidemic lately. The cause is likely some kind of dynamic/pulsing issue caused by the larger injectors, and the fix is more fuel system volume. That's not more volumetric flow, just more volume in the fuel system. Larger rail, larger lines, larger filter, etc, anything that increases fuel system volume. Here's what I've found so far, with the help of some really awesome remote tune customers that were willing to swap out parts and spend some cash to collectively solve this decade old mystery.
​
-
No single part is a fix for this (including dedicated pulse dampers like Radium (more testing is being done on these)), but the combination of a few parts that increase system volume. Every individual part was tested by itself and none were an obvious fix on their own.
-
The issue is definitely tied to larger than stock injectors, but not any specific size or brand. Everything from 650 to 2150s has caused this problem. Going back to stock injectors fixes it, but of course, that is not a real solution. Just proves that it is injector driven.
-
We've found that teeing in a dead ended hose about 5 feet long at the rail does provide a lot of damping and mostly solves this issue. But that's a pretty untidy solution and most people aren't going to want to do that. It just illustrates the point that more system volume is the answer. This acts like a water hammer arrestor in home plumbing systems and provides pulse damping.
-
Upgrading to a -8 feed line, and ideally the filter and rail as well, has been shown to be totally effective, and you get the added benefit of increase flow from those bigger pumps at the same time. A -6 feed line is not a complete fix, it's better than the stock feed line but not as good as the -8 line. I've always felt a -6 line is fine for 450/525 pumps, but for this reason alone I now recommend -8.
-
Commercially available Fuel Pulse Dampers did not help on two different cars.
​
​
This example is of a set of 1650s on stock rail and stock lines with a 450 pump. It was much worse on 2150s, off by 40% at the peak of the wave.
​
​
​
​
​
​
​
​
II sent out a ~5 foot length of -6 line to tee in next to the fuel rail as a test (other end capped off, just to add fuel system volume). This was the result of that change. Most of the AFR wave was eliminated and VE dialed in normally. It was approximately a 10% change at the peak.
​
​
​
​
​
​
​
​
This is the same wave that results in MAFcomp tuning with this issue.
​
​
​
​
​
​
​
​
​
​
​
​
​
This car is on 2150s, 450 pump, stock rail and lines. The AFR wave is obvious in the green trace. Less obvious is that it also seems to affect idle on this car.
​
​
​
​
​
​
​
​
More to come...
​
​
​
Modern injectors and filtering:
​
Recently I had a new issue with my own car. It runs two sets of FIC High Z 1650s, my all time favorite injector. All modern small body Bosch injectors are more sensitive to debris than older injectors. A 10um filter is the minimum required for these injectors, and finer is better. I use a stainless 100um pre filter right off of the 1 gallon fuel cell, and a 10um stainless filter post mechanical fuel pump. I ran this way for many years trouble free. But, recently, I started having chronic injector issues. After a long period of troubleshooting, replacing lines, etc, I found the internals of the mechanical pump rusting. The rust will eventually clog the 10um filter (and indeed the pump then crushed it due to the restriction), and some of that rust gets through it and leaves a fine residue on everything. 4 and 4 micron filter systems are available, but very expensive. I may still do it, because this has been a major pain in the ass and has cost me one engine. At any rate, the pump needs to go back for service.
​
Here is some individual cylinder AFR data that highlights the issue at a glance.
​
Dirty Injectors:
​
​
​
​
​
​
​
​
​
​
​
​
​
​
​
​
​
​
​
​
Clean Injectors:
n
​
​
​
​
​
​
​
​
​
I
​
​
​
​
​
​
​
​
​
I also had an issue wth M5 methanol swelling up the rubber check ball in my pre-pump check valve. This took a minute to find, but the drop in base pressure in the logs was obvious. It would run fine at idle, but did not pass enough fuel to run it much over idle.
​
When it was first removed, it was almost the same diameter as this part that threads into the body of the checkvalve.
​
​
​
​
​
​
​
​
​
​
​
​
​
​
​
​
​
And after sitting out for a day to outgas:
​
​
​
​
​
​
​
​
​
​
​
​
​
​
​
​




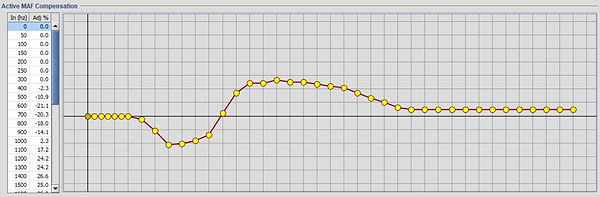



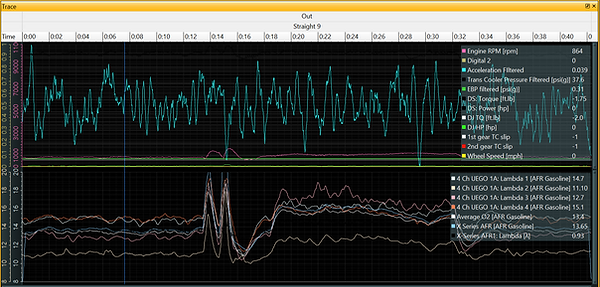


